What inspection methods are commonly used for spray nozzle maintenance?
As an example, the spray nozzle inspection method described here uses only a few selected applications, but can be used as a guide to determine other application inspection methods based on determining the order of quality control requirements in each particular application.
1. Traffic
· Flowmeter reading
· Collect the amount of liquid in a graduated container or measuring cup
2.Pressure
· Pressure gauge reading
· Check spray status
3. The spray shape
· Measure the Angle with a protractor
· Spray width is measured on spray section
· Visually inspect the uniformity of spray shape
· Check spray shape with special equipment for critical applications
4. The quality of the product
Check for uneven coating coverage
Check for signals of uneven cooling in cooling applications (e.g. on thin steel plates)
In spray drying, check particle size and moisture content
5. Application effect
In flue gas cooling, check the outlet flue gas temperature;
In dust control, check the dust content in the environment;
Humidify the spray and check the relative humidity in the room.
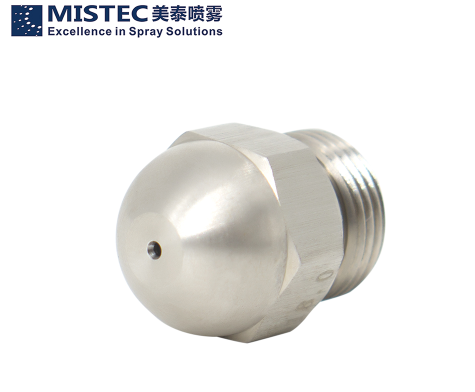
To answer this question, two main factors need to be considered:
Wasted water;
Chemicals and electricity
Final product quality;
Rework.
Performance guarantee and after-sale service fee.
In dust control;
Spray humidification;
Flue gas spraying and cooling;
In the application of spray drying without direct contact with the products produced, the negative effect on the application effect is to cause unwanted problems and costs, such as environmental penalties.
Based on experience in each particular application, the operator can determine whether continuing to use the problematic spray nozzle adds additional costs: if so, the spray nozzle should be replaced.
After a certain period of production operation, the replacement standard of spray nozzle can be determined on the basis of regular inspection.
For example, a 15% increase in flow rate above the design value should be a signal to change the spray nozzle
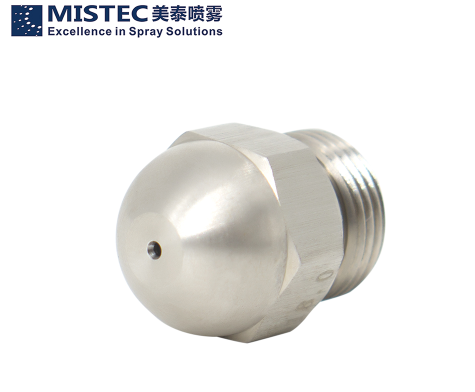
spray nozzles should be replaced, but for how long?
Wasted water;
Chemicals and electricity
Final product quality;
Rework.
Performance guarantee and after-sale service fee.
In dust control;
Spray humidification;
Flue gas spraying and cooling;
In the application of spray drying without direct contact with the products produced, the negative effect on the application effect is to cause unwanted problems and costs, such as environmental penalties.
Based on experience in each particular application, the operator can determine whether continuing to use the problematic spray nozzle adds additional costs: if so, the spray nozzle should be replaced.
After a certain period of production operation, the replacement standard of spray nozzle can be determined on the basis of regular inspection.
For example, a 15% increase in flow rate above the design value should be a signal to change the spray nozzle