Industry: Manufacturing
Business content: bottle caps, bottles, cartons, electroplating tin sheet steel processing, sales
Case Background:
China's glass manufacturing industry has a long history. Since the reform and opening up, the glass manufacturing industry has developed by leaps and bounds in both output and quality.
At present, China's glass products account for about 50% of the global output, and a large number of glass products are exported overseas every year.
As the industrial fuel of glass melting kiln in China generally uses heavy oil, therefore, the flue gas emitted by glass furnace contains a large number of nitrogen oxides, sulfur dioxide and other pollutants, which are the main sources of air pollutants, direct emissions will cause serious air pollution.
According to the strategic deployment guidance of the 16th CPC National Congress and the development requirements of the 11th Five-Year Plan, the glass manufacturing industry should speed up the upgrading of industrial structure, constantly improve the efficiency of resource utilization and reduce the emission of pollutants.
Under the requirement of this era background, the flue gas control of glass furnace will be urgent, and it is also an important way to achieve the goal of cleaner production.
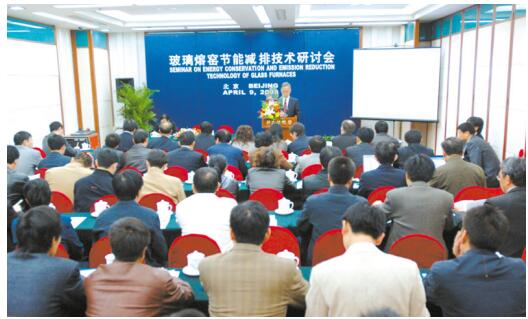
Glass melting furnace for glass manufacturing industry must have a melting deviceIn the production process, the flue gas pollutants have high temperature, moderate flow rate, high SO2 content and low dust content.
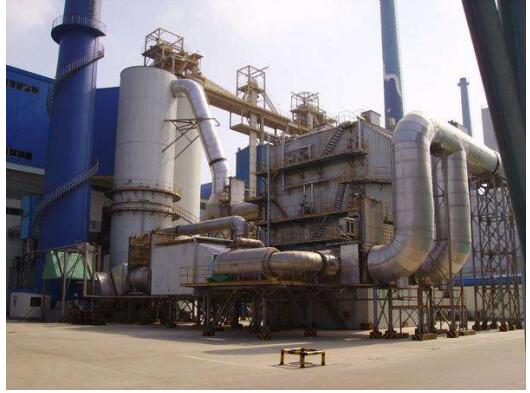
Topic: The waste gas and dust produced by the glass furnace need a suitable nozzle to spray lime water to desulphurize the dust, so as to avoid excessive discharge, so as to meet the requirements of the environmental protection standard of the enterprise.
Anshan Yongan glass bottle Factory used to use large flow silicon carbide nozzle, there are many problems, hope to find through Mattel desulfurization and dust removal effect can meet the discharge standard of the program and nozzle.
Recommended products: AA standard hollow cone nozzle
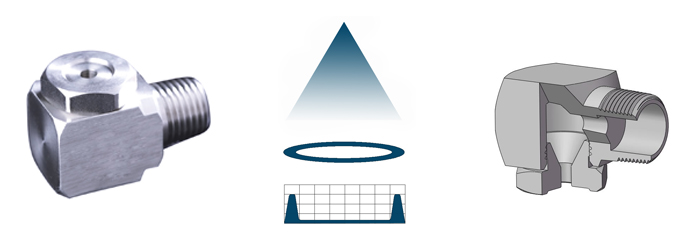
Improvement: the gas emission is within the limits of the pollutant emission stipulated in the environmental protection emission regulations of the Glass Industry Air Pollutant Emission Standard (GB26453-2011).
Past flue gas treatment methods:
In order to reduce the dust and sulfur dioxide in the discharge, Anshan Yongan glass bottle Factory firstly adopts wet dust removal with large flow silicon carbide nozzle.
The structure of silicon carbide vortex nozzle and swirl cavity is used to produce hollow conical core spray with large flow rate.
There are many problems in the use of silicon carbide vortex nozzle:
The required pressure and flow are relatively large, the current two pumps of Anshan Yong 'an Glass Bottle Factory cannot meet the requirements, and the cost of pump replacement is high.
Spray particle size is relatively coarse, can not reach the dust removal effect;
The silicon carbide nozzle has large flow, large lime water consumption and high operation cost.
The selection of nozzles for comprehensive treatment of flue gas in glass furnaces should follow the following principles:
Design nozzles for existing pump head and flow
1. The flue gas regulation conforms to the requirements of the state environmental protection department and the local government for flue gas treatment efficiency
2. The nozzle is resistant to high temperature, wear and tear, and is not easy to plug, easy to replace the operation, long life.