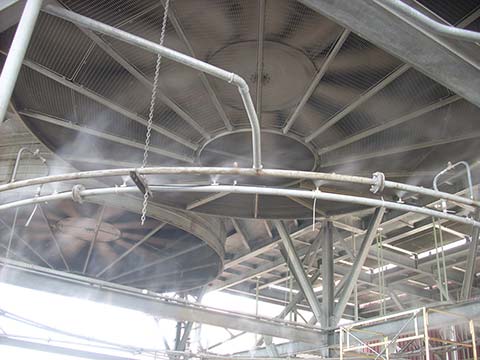
Atomizing spray generation
Atomizing spray can be produced by a variety of ways, but regardless of which way, there are a few basic factors that apply to all atomization processes:1. The development of surface waves atomizing sprayed by circular jet or liquid film jet and the disturbance effect of gas involve the formation and development theory and aerodynamics of jet surface waves, which will lead to the fragmentation of jet liquid into sheets, lines, large particle droplets, and eventually small particle droplets.
2, the geometry of the atomizing spray nozzle, the flow characteristics inside the atomizing spray nozzle, the difference between the atomizing spray pressure and the ambient gas back pressure, the nature of the gas medium and the physical characteristics of the liquid itself, they are crucial to determine the atomizing spray shape, cone Angle, penetration, droplet size and velocity distribution over time and space. These factors do not exist independently, but interact and complement each other, and ultimately determine the effect of atomization.
The study of atomizing spray mechanism has always been one of the difficulties in atomizing spray science and has not yet been perfected. The establishment of physical and mathematical models requires researchers to have solid knowledge of fluid mechanics and mathematics. The correct determination of various boundary conditions and the rigor of mathematical derivation are very demanding, and sometimes even need to be repeatedly discussed before progress can be made.
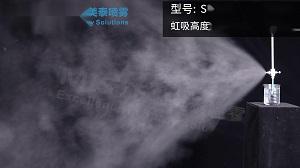
Atomizing spray nozzle
According to the shape and characteristics of the atomizing spray nozzle can be divided into many types, each nozzle has its specific purpose and atomization characteristics. The most typical nozzle is the flat-hole atomizing spray nozzle, which is widely used in the combustion chamber of automobiles, aircraft and rocket engines. The circular jet formed by the flat hole atomizing spray nozzle is atomizing sprayed out at high speed under high injection pressure, and is broken by the disturbance of the air flow.The atomizing spray principle of the nozzle:
As long as the wavelength of the surface wave of the liquid circular jet is close to twice the diameter of the circular jet, the disturbance of the flow will lead to the fragmentation of the circular jet. However, the turbulent circular jet can be broken only by its own turbulent pulsation without any external force. Once the liquid leaves the atomizing spray nozzle, the nozzle wall no longer controls the circular jet, and the liquid will be directly affected by its own surface tension.When the liquid overcomes its own surface tension, the circular jet breaks apart. The liquid reaches a new equilibrium in the form of small sheets, lines, or droplets of particles, and as soon as the liquid overcomes the surface tension again due to perturbations by itself or by the gas, it breaks further into finer particles. The viscosity of liquid inhibits the growth of circular jet instability and delays the process of liquid fragmentation, so that atomization occurs in the downstream region where the velocity of gas and liquid is low.
In most cases, the turbulence of the liquid, the cavity of the nozzle, the increase of the ambient gas density and the aerodynamic action are all favorable for atomization. The nozzle that can produce the liquid film jet atomizes the liquid and makes the liquid and gas fully mixed.
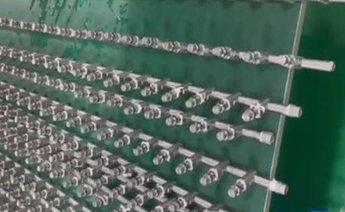
Effect of nozzle on liquid film jet:
Planar film jets are usually produced by high-pressure liquid passing through a slit, such as a fan atomizing spray nozzle, which is used in the garment industry and in small annular gas turbine combustors.Annular liquid film jet is produced by high-pressure liquid passing through an annular slit, such as the needle nozzle in the pressure atomizing spray nozzle and the pre-film nozzle in the jet atomizing spray nozzle, which are used in diesel engine and gas turbine respectively. Or produced by a turntable or cup, called the turntable atomizing spray nozzle and the cup atomizing spray nozzle, respectively, for atomizing drying, atomizing cooling and agricultural irrigation. These atomizing spray nozzles require a certain injection pressure or rotational centrifugal force in order to produce a certain injection speed.
Once the liquid film jet is formed, its initial hydrodynamic stability will be destroyed by the aerodynamic disturbance. With the expansion of the liquid film jet away from the nozzle, the thickness of the liquid film jet will gradually increase, causing it to break into liquid lines and final droplets. If the injection pressure is large enough, the liquid will atomize into fine particles at the exit of the nozzle, and there is no linear transition zone.
In addition, the initial thickness of the liquid film jet, the relative velocity with the ambient gas, the viscosity of the liquid and the surface tension are also important factors that determine the size range and average diameter of the atomized droplets. There is a high relative speed between the liquid atomizing sprayed by the jet nozzle and the ambient gas, and the liquid movement speed is slow, while the jet air speed is fast and the flow rate is large. The basic mechanism is that the low-viscosity liquid is ejected by the low-pressure atomizing spray nozzle with the high-speed jet, and the surface wave of the liquid film jet breaks and atomizes due to the disturbance of the high-speed jet stream.
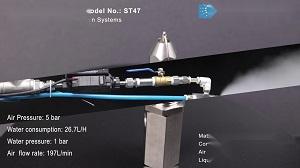
Atomizing spray characteristics
The shape, divergence, cone Angle and penetration distance of atomizing spray liquid beam are collectively referred to as atomizing spray characteristics.atomizing spray beam configuration:
In most practical applications, the symmetry of atomizing spray beam morphology is an important parameter. The asymmetric liquid beam weakens the efficiency of liquid fragmentation and makes the atomization quality worse. In atomizing spray printing and dyeing, the symmetry and uniformity of the liquid bundle are the basic requirements to ensure the printing and dyeing quality.
The symmetry of the beam is also very important for the atomizing spray in the combustion device, the fuel must be evenly distributed throughout the combustion chamber space, so that the fuel and air can be fully mixed, improve combustion efficiency, reduce emissions of pollutants. However, asymmetries in the atomizing spray stream are usually not noticeable until the asymmetry is very severe.
The divergence of the atomizing spray is the ratio of the total volume of liquid and gas in the atomizing spray to the volume of liquid in the atomizing spray. The liquid beam with high divergence can make the mixing of atomized liquid and ambient gas more rapid, and the evaporation rate of liquid droplets is higher.
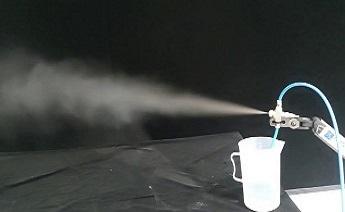
Atomizing spray divergence and atomizing spray cone Angle:
The divergence is closely related to the atomizing spray cone Angle, and the atomizing spray cone Angle of the flat hole atomizing spray nozzle is small, and the divergence is also small. In general, the factors that increase the atomizing spray cone Angle will increase the divergence of the beam.Because of the interaction between the atomizing spray liquid beam and the ambient gas, the boundary of the atomizing spray liquid beam is not straight, but a curved surface, which makes it difficult to define and measure the atomizing spray cone Angle. In order to solve this problem, the curve of the liquid beam profile is usually replaced by a straight line connected from the atomizing spray nozzle outlet to a certain axial position of the liquid beam.
To measure the atomizing spray cone Angle with flash photography, it is usually necessary to enlarge the side photo of the liquid beam at least 2-3 times, so that the measurement results are more accurate. A simple measurement method is to place a piece of white paper in a certain axial position of the liquid beam, the atomizing spray will wet the white paper, immediately measure the diameter of the wet blot on the white paper, and the atomizing spray cone Angle can be obtained by simple calculation.
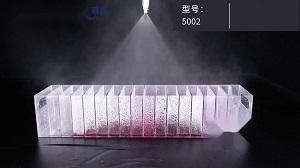
Penetration distance of atomizing spray:
The penetration distance of the atomizing spray can be defined as the maximum distance that the beam can reach. It is determined by the difference between two interacting forces: one is the initial force of the liquid jet, and the other is the aerodynamic resistance of the ambient gas.The initial velocity of the jet is very high, but with the progress of the atomizing spray process, the increase of the number of atomized droplets and the increase of the total surface area, the kinetic energy of the liquid is gradually weakened due to the friction between the droplets and the ambient gas. When the droplet's kinetic energy is finally exhausted, the droplet will move with the movement of the ambient gas, or fall due to gravity. The greater the injection pressure, the smaller the ambient gas resistance, the smaller the atomizing spray cone Angle, and the larger the penetration distance.
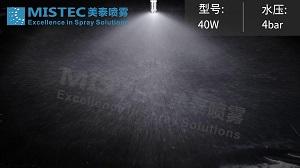
Atomizing spray atomization
Typically, atomized droplets come in a wide range of sizes. Knowledge of droplet size distribution is useful for evaluating atomization mass and for calculating mass and heat transfer between droplet and ambient gas.The difficulty in determining the size distribution of atomized droplets leads to the use of an easily determined average diameter to evaluate the quality of atomization. The average diameter of atomized droplets is usually expressed in swelling and can be expressed in a variety of ways. Such as length average diameter D10, surface area average diameter D20, surface length ratio average diameter D21, volume average diameter (or mass average diameter)D30, body length average diameter D31, Sauter average diameter D32(or represented by the symbol SMD) and DeBmuckere average diameter D43, etc. The most commonly used is the Sauter mean diameter, especially for mass and heat transfer problems in the combustion chamber, which is used to evaluate, followed by the volume mean diameter and the length mean diameter.
Evaporation will make the large particle droplets atomized smaller, and the small particle droplets become a gas, that is, the particle size is zero. It, together with the droplet collision, directly affects the droplet lifetime, thereby redistributing the droplet size over time. It is of great significance for evaluating the atomization quality of fuel in the combustion chamber over time, and it also has a great influence on the emission of combustion products.
There are many methods to measure atomization characteristics and droplet size distribution. The most advanced methods include laser holography, high-speed photography, laser Doppler and Malvern method. The exposure time of laser holography is very short, which can record three-dimensional transient images of atomizing spray particles and reproduce them statically. The frequency of high-speed photography can reach more than 100,000 frames per second, and with computer image processing software, it can also be used to study atomizing spray characteristics such as atomizing spray speed, cone Angle, and penetration distance. Laser Doppler and Malvern particle analysis system can accurately and efficiently study the size distribution of atomized droplets. The common disadvantage of these measurement methods is the higher price of high-quality instruments.
In recent years, high-definition digital cameras have developed rapidly, and high-end products are constantly updated. It has the advantages of convenient shooting, high reliability, easy adjustment of shooting position and parameters, clear image, low test cost, and can be used for comparative study of atomizing spray characteristics.
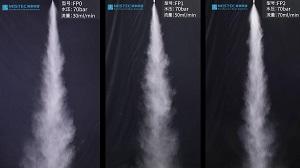
Atomizing spray application
Natural atomization includes rain, waterfalls and seawater atomization. The application of atomizing spray mainly has the following aspects:1. Daily life: shower, garden and grass watering, hair atomizing spray and mousse for hair styling, mosquito and fly atomizing spray and air disinfection, cleaner, air humidifier, street cleaning sprinkler, atomizing spray painting, inkjet printer, etc.
2, medical: atomizing phlegm remover and evaporation of volatile anesthetic, etc.
3. Production and process flow: Atomizing drying (such as milk products, coffee and tea, tablet icing, soap and detergent, etc.), atomizing wetting, atomizing cooling (such as atomizing tank, tower, reactor, etc.), atomizing reaction (such as absorber, dryer and car paint room), powder metallurgy, surface grease (such as epoxy resin, polyester, etc.), foam and emulsifier preparation, car cleaning nozzle, etc. Clothing (including surface treatment, atomizing spray printing and dyeing, fiber and insulation material production, etc.), acid and alkali etching of semiconductors and computer chips.
4, agriculture: to atomizing spray the fruit tree pesticide atomizing sprayer and agricultural irrigation, use the atomizing sprayer for crop water supply than the water flood irrigation to save more valuable water resources, and the growth of crops is good, this method requires that the size of the atomized droplets can not be too small, in order to
atomizing spray farther to increase the area covered by irrigation.
5, fire: atomized water droplets can absorb more heat, so as to effectively suppress the fire.
6, asphalt atomization paving: (often manifested as non-Newtonian fluid).
7, combustion chamber: fuel atomization of oil-fired boilers, diesel engines, gasoline engines, gas turbines, aircraft engines and rocket engines. In these devices, the design and manufacturing precision of the atomizing spray nozzle is very high, and the atomized large number of small particle fuel droplets can effectively increase the surface area of the fuel and the accelerant contact, so that the fuel evaporates rapidly, and is fully mixed with the accelerant, enhancing the transfer of mass and heat and burning completely, reducing emissions and pollution.