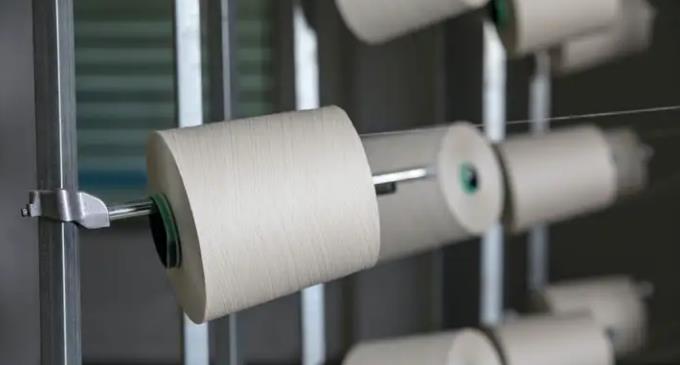
In the pre-spinning process of flax, humidity is very important to the texture and processing properties of the fibers. High pressure atomizing system humidification system through precise control of humidity, improve fiber softness and toughness, reduce breakage and damage, improve product integrity and quality, while environmental protection and energy saving, contribute to the sustainable development of enterprises and green production.
It is very important to control fiber moisture in the pre-spinning process of flax. Too high or too low humidity will adversely affect the texture and processing properties of the fiber. The high-pressure micro-fog humidification system provides an ideal processing environment for flax fibers by precisely controlling humidity.
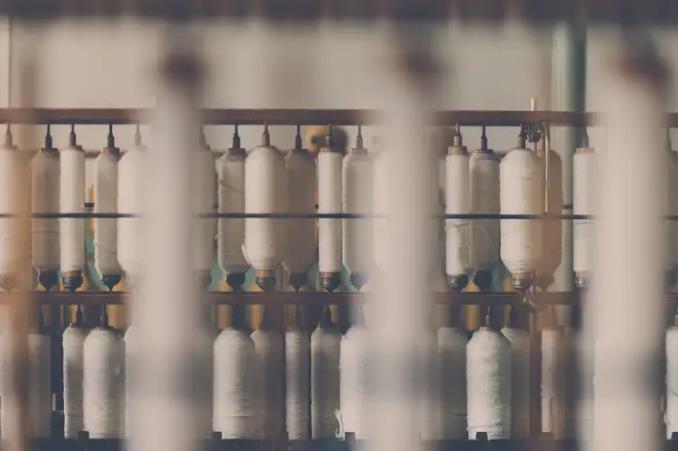
1. Influence of pre-spinning process humidity
In the pre-spinning process of flax, the workshop humidity is directly related to the softness and elongation of the fiber, and is also closely related to the electrostatic phenomenon. When the humidity is too low, flax fiber is difficult to stretch and comb, and it is easy to generate static electricity, resulting in fiber adsorption parts, which seriously affects the textile process. In addition, too low humidity will also make the roller and other parts hard, further increasing the difficulty of spinning.2. Humidification effect of micro-fog system
The high pressure atomizing system humidification system provides suitable humidity environment for flax pre-spinning process. By high pressure to fine the water into tiny droplets, these droplets can be quickly and evenly dispersed in the air, for flax fiber humidification treatment provides an ideal condition. In such a humid environment, the softness and toughness of flax fibers are significantly improved, thus reducing the fracture and damage during processing, and greatly improving the integrity and quality of the product.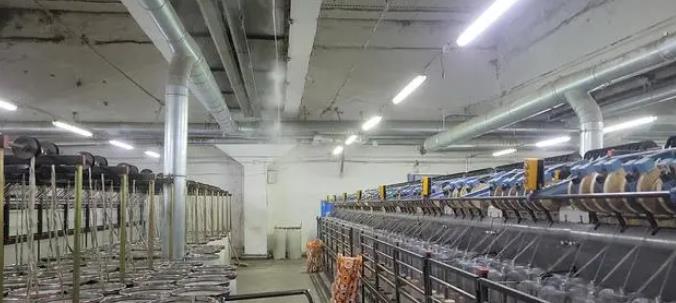
3. Micro fog system environmental protection and energy saving
The high-pressure micro-fog humidification system has high efficiency atomization ability, which greatly improves the utilization rate of water resources and avoids the waste of water resources. At the same time, because the droplets are very small and uniform, they can quickly reach the required humidity and remain stable, reducing energy consumption. This environmental protection and energy saving characteristic not only conforms to the development trend of modern industry, but also provides strong support for the sustainable development of enterprisesThe installation of high-pressure micro-fog humidification equipment in the linen pre-spinning workshop can not only improve production efficiency, ensure product quality, but also contribute to the sustainable development of enterprises and realize green production.
Why humidification in textile manufacturing
Humidification and humidity control in textile manufacturing
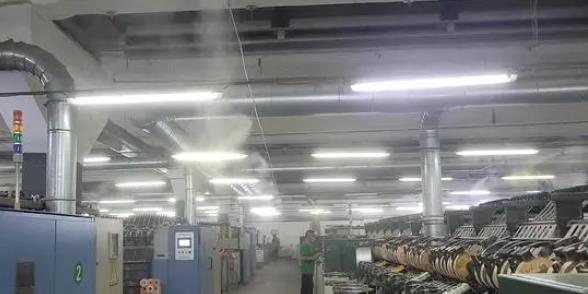
The textile industry understands that the integrity of its products is of Paramount importance. When fibers and fabrics are at their best, they increase strength and comfort. However, because they are hygroscopic, this means that they release and absorb moisture from the surrounding air. Textiles are inherently sensitive to changes in relative humidity. Under low humidity conditions, the fabric will release moisture, resulting in weakening, affecting elasticity and tensile strength.
Just as troublesome to deal with these products is static electricity. The lack of moisture in the air and the material itself will increase the resistance, which will produce static electricity, which will be released to the machine and even people. This can also cause products to stick together, which affects production time and quality.
With consistent water drop levels, the fibers have the conditions needed to maintain optimal quality during production, and preventing water loss during textile processing and storage can reduce weight loss from a typical 4% to 0.5%. Proper humidification will maintain yarn strength and elasticity, producing better quality products with higher profit margins. Optimum humidification reduces yarn breakage during weaving, machine downtime, loom stop marks and weaving in the finished product.
Humidification systems in the textile industry not only improve products, but also improve safety. Static electricity can lead to reduced productivity and product quality due to lint and fly attraction, machine clogging and employee discomfort or even accidents. Higher humidity naturally dissipates the static charge, alleviating these problems. The humidifier provides evaporative cooling of approximately 5°C to textile production facilities while suppressing dust, fleece and lint, the combination of higher humidity increasing particle weight and the evaporative cooling effect creates downward air flow for a cleaner, healthier working environment. Employees have fewer respiratory illnesses and less particulate matter in the environment.