1. Preface
The nozzle is a part of the coating pretreatment equipment and the core of the spray system. Spray treatment method is one of the common process methods before coating treatment, the process is to spray the tank liquid to the surface of the workpiece with the help of mechanical flushing, accelerate the chemical action, to complete the degreasing, rust removal, surface adjustment, phosphating and passivation and other processes, so that the degreasing effect is better, the phosphating film is more uniform, the processing time is shorter, and the production efficiency is higher. For different workpieces, when selecting the nozzle type, there are more factors that need to be considered comprehensively, and the correct choice can give full play to the performance of the coating pretreatment agent and its own characteristics, and obtain high-quality pretreatment effects.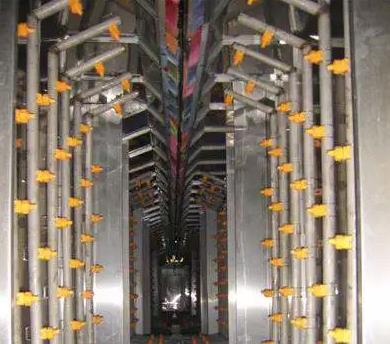
2, Nozzle characteristics
Because the nozzles are designed to operate under a variety of different spray conditions, the appropriate nozzles are selected to achieve the best spray performance in use.The characteristics of the nozzle are mainly reflected in the spray type of the nozzle, that is, the shape of the liquid when it leaves the nozzle mouth and its operating performance. The name of the nozzle is divided into the spray shape of fan, cone, liquid column flow (that is, jet), air atomization, flat nozzle, cone nozzle is divided into hollow cone and solid cone two categories; The naming of Venturi nozzles (that is, mixing nozzles), strong cold (hot) tuyere blowers and special nozzles (such as garden nozzles, cylinder washing nozzles, pipe cleaning nozzles, etc.) reflects the operating performance of nozzles.
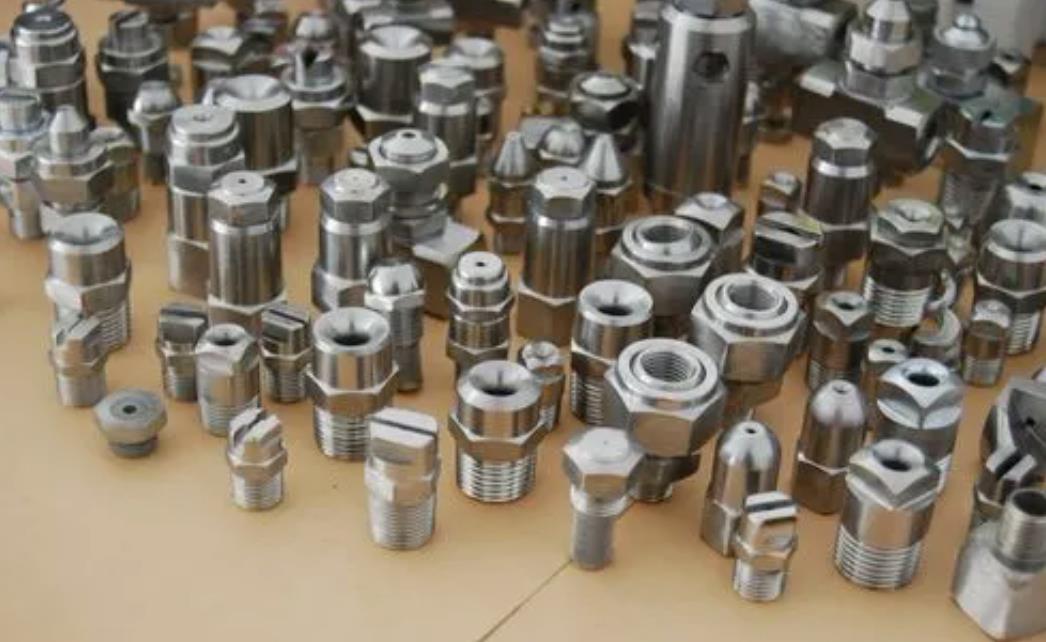
3. Select the elements of the nozzle
There are more types of nozzles and a larger range of choices. Generally speaking, the nozzles of degreasing and washing processes can choose jet nozzles with strong impact force: Take "V" type or fan type nozzle as an example, the jet Angle is the best to 60°, which has a larger impact force; The nozzle of the phosphating process can choose a centrifugal nozzle with good atomization, fine and uniform water particles and weak impact force: take the "Z" type conical nozzle as an example, the best distance from the nozzle to the workpiece is 40cm ~ 50cm, which has a dispersion and spray effect of liquid atomization. The arrangement of nozzles on the nozzle can be in parallel and cross two forms, and the vertical cross arrangement is used for the passage type, which has better spray effect.The factors that choose the nozzle are flow rate, pressure, spray Angle, coverage, impact force, temperature, material, application, etc., and these factors are often implicated and mutually restricted. Flow and pressure, spray Angle and coverage are proportional. The purpose of spraying any nozzle is to maintain continuous contact between the tank and the workpiece, and the flow rate is more important than the pressure. The temperature of the liquid does not affect the spray performance of the nozzle, but it affects the viscosity and specific weight, while also affecting the choice of materials. The material of the nozzle should also be determined according to the chemical characteristics of the tank, and the non-corrosive tank can be cast in bronze or plastic according to the difficulty of processing. To prevent corrosion, non-gold materials can be used; For sulfuric acid, hydrochloric acid and other strong corrosion tank liquid, nylon plastic can be used; The nozzle material for phosphating tank is generally made of acid-resistant stainless steel, and the nozzle to prevent rust can also be directly made of stainless steel or nylon.
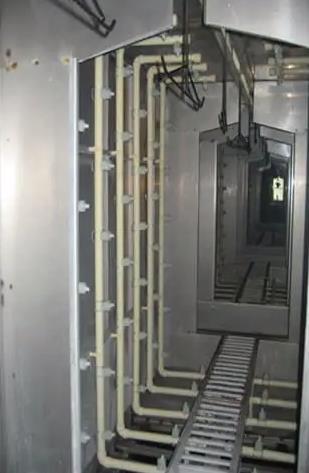
4, Nozzle arrangement
A number of nozzles are installed in a certain arrangement on the ring pipe composed of the outer dimension of the workpiece, and the workpiece is surrounded so that all the surfaces of the workpiece can be sprayed by the tank liquid when it passes through the spray area. The nozzles should be evenly arranged throughout the spray area to ensure the process time and effect of the spray washing. The distance between the nozzle and the workpiece should be within the optimal diffusion range of the jet, so the nozzle and nozzle arrangement should be reasonable. The distance between the nozzle and the nozzle is 250mm ~ 300mm, and the distance between the nozzle and the workpiece is preferably not less than 250mm when cross-arranged. ?? A complete tank spray system is formed from the pump to the pipeline to the mixing nozzle. Stirring nozzle uses Venturi principle, the groove liquid enters the pipeline under a certain pressure, forms a high-speed jet through the nozzle hole of the stirring nozzle, and produces a low pressure area around the nozzle inlet, forming a siphon phenomenon, and under the action of pressure difference, the groove liquid is sucked into the stirring nozzle, so as to circulate a large amount of liquid. The distance between the mixing nozzle and the bottom of the groove is 25mm ~ 75mm, and the distance between the nozzle and the workpiece is 200mm ~ 380mm, and the Angle of the nozzle hole should be determined according to the size of the workpiece. When the workpiece width is small, the spray hole can be designed vertically upward, when the workpiece is large, the spray hole can be designed to be 35° ~ 45° with the vertical plane; When the width of the workpiece is large, in order to improve the mixing effect, the spray hole can be designed vertically downwards, but this situation will stir up the sediment, so it is only suitable for mixing without sediment tank liquid.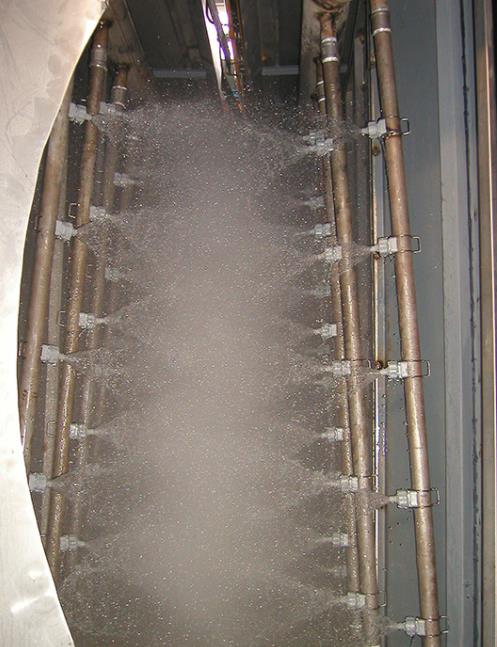
5, Nozzle quality inspection and the common causes of damage
The nozzles need to be serviced, regularly inspected, cleaned and even replaced in order to ensure the quality of the final product and maintain the economic efficiency of the production process. The mode and frequency of maintenance procedures depend on the use. Maintenance schedules can be arranged according to application, liquid and nozzle material.There are seven common causes of nozzle spray problems:
a) Corrosion and wear: the material on the surface of the nozzle nozzle and the internal flow channel gradually becomes larger or deformed, which affects the flow rate, pressure and spray shape.
b) Corrosion: The spray liquid or the chemical action of the environment causes corrosion to destroy the nozzle material.
c) Blockage: Dirt or other impurities in the liquid block the nozzle mouth, thus limiting the nozzle flow and interfering with the spray shape and its uniformity.
d) Bonding: Splash, mist or chemical buildup caused by liquid evaporation on the inner or outer material of the nozzle edge, which can leave a dry solidified layer and block the nozzle or internal flow channel.
e) Temperature damage: overheating will have a certain damaging effect on nozzle materials designed for non-high temperature purposes.
f) Incorrect installation: off-axis gaskets, over-tightening or other positional changes can have adverse effects.
g) Accidental damage: During installation and cleaning, the nozzle may be accidentally damaged due to the use of incorrect tools.
6, The application field of nozzle
1, all kinds of cleaning machines in the automobile manufacturing industry, spray cleaning in the coating line, atomizing spray, tank mixing and other equipment.2, motorcycles, bicycles, refrigerators, washing machines and other manufacturing in all kinds of cleaning machines, painting lines.
3, various cleaning equipment in the mechanical processing industry.
4. Humidification device in light textile industry.
5, cleaning machine manufacturer, painting equipment manufacturer supporting nozzle.
6. Nozzle for agricultural sprinkler irrigation and urban greening.