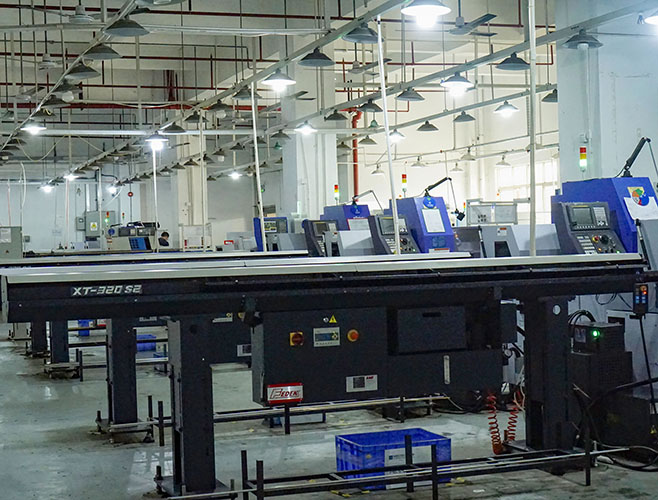
Heat treatment process:
Heat treatment is a process method that uses solid state heating, insulation and cooling methods to change the internal organization of steel parts, so as to improve the performance of steel, but does not change the chemical composition and shape of steel. Heat treatment process can also be divided into ordinary heat treatment, such as annealing, normalizing, quenching (also known as hardening treatment), surface quenching, tempering and aging process methods; And chemical heat treatment, that is, during the process of heating and holding the workpiece in the medium of the furnace, the active atoms in the medium permeate the surface layer of the artificial part to change the surface chemical composition and organization, so that the surface has special mechanical, physical and chemical properties, such as carburizing, nitriding and cyaniding process methods.Some of these methods are also used for nozzle parts, as shown in Table 5. 120 describes the application of some typical zero loads. The process in the table is a long-term production workshop out of the conventional general process specifications, but according to the material properties, parts shape and size to determine the low failure rate of the process and its parameters.
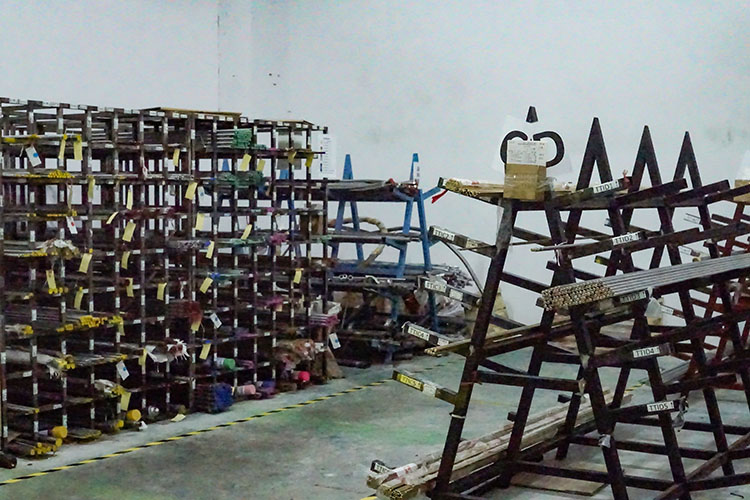
Surface treatment process:
The surface treatment process is to attach a covering layer to the surface of the part to achieve rust prevention, decoration and other purposes. Generally divided into three major
Category: Electroplating, such as chrome plating, nickel plating, cadmium plating, zinc plating, etc. Surface chemical treatment, such as oxidation, phosphating, commonly known as blue, hair (yellow) black is actually oxidation; Paint it. Some metal parts of the nozzles need to be corrosion resistant, so different surface treatment processes are used according to different working environmental conditions.
The processing accuracy of all precision parts (including dimensional tolerances, shape and position tolerances, etc.), surface roughness (or commonly known as finish), surface hardness (anti-abrasion), anti-corrosion, etc., have strict requirements. In addition, these precision parts and other parts of the nozzle assembly also have strict requirements. Therefore, the manufacturing process of nozzle precision parts has become one of the keys to nozzle technology, and it is also reasonable. The processing requirements and processes of typical parts will be further introduced.
Nozzle manufacturing process technology with the progress of science and technology and machinery manufacturing technology and equipment is also constantly developing and improving, highlighted in the following aspects:
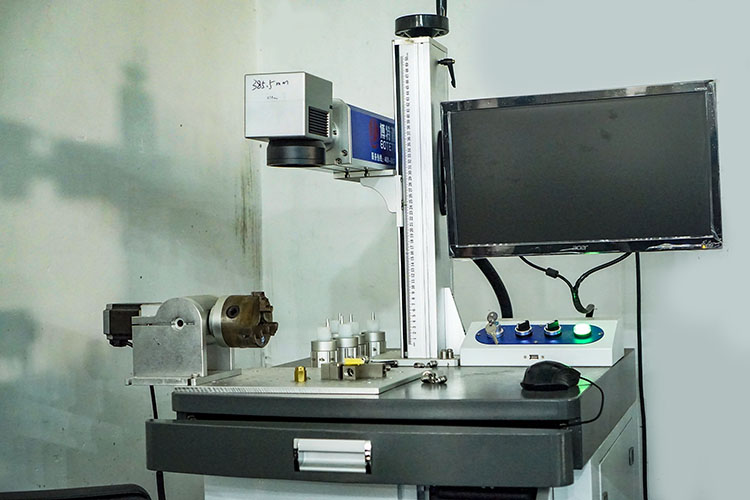
Blank refinement technology, that is, precision casting (forging) blank instead of rough casting (forging) blank. Especially no spare or small spare precision casting, can save expensive raw materials, reduce processing hours, reduce production costs; It is also possible to rely on precision molds to ensure more complex geometric shapes and dimensions. The key of the precision casting process lies in the manufacture and inspection of precision molds, as well as the melting and pouring of materials. At present, these technologies are no longer a problem, because of this, the use of plastic injection nozzle is very accurate and beautiful.