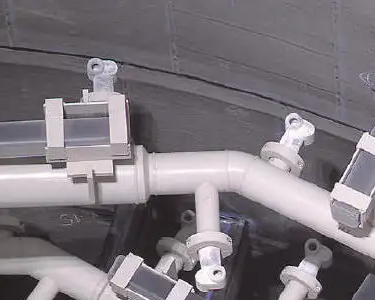
In daily production, due to the different nozzle material and use environment, the corresponding inspection and maintenance will also have a certain difference. Usually, we determine the appropriate inspection frequency based on the purpose of the nozzle, and the material of the nozzle, the nature of the tank treated, and so on ultimately determine the nozzle repair and replacement plan.
Problems with nozzles include:
1, nozzle bonding:When the liquid through the nozzle is accelerated to evaporate for various reasons, a dry solidified layer is left behind on the edge of the nozzle mouth, including the inside and outside sides, because of splashing, atomization and chemical reaction. This is also the after-effects that the nozzle has to face for a long time. The result of the sticking of the nozzle is the blockage of the water outlet hole or the inner flow channel. Some of this blockage can be dredged by manual maintenance, but most application units are subject to cost or the effect of dredging, and usually choose direct replacement. Because after the stain at the scale point is hardened, it is difficult to dispose of it without damaging the nozzle.
The correct treatment method after the binding of the nozzle is to soften the stain first, and then clean it slightly by a soft brush, or blow it off with compressed air. When doing this work, the cleaning point and cleaning intensity are very critical. Once the nozzle damage is caused, it cannot be repaired later, and the problem can only be solved by replacing the nozzle.
2. Blockage of nozzle:
In the long-term spray process, the nozzle is often recycled liquid, coupled with the treatment gas contains a certain amount of solid dust, so the dirt and impurities in the tank will gradually accumulate in the nozzle mouth or the internal flow pipeline, resulting in nozzle obstruction.
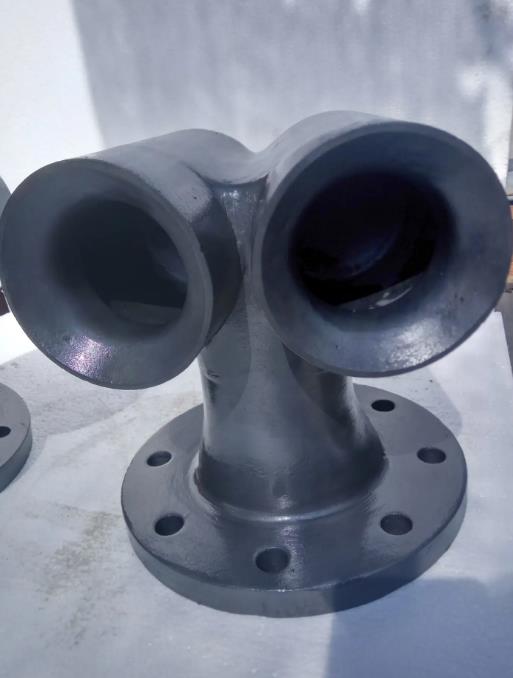
If the sticking of the nozzle will cause the flow rate to become smaller, it will affect the spray pressure, the shape of the spray and the uniformity of the liquid particles. The blockage of the nozzle will be more serious. Once blocked, it may burn out the pressurized pump or make the nozzle link loose under high pressure, or even the nozzle collapse. This type of risk usually causes more damage, so you should strengthen the observation, or choose a nozzle model that is not easy to clog in the initial selection.
3. Corrosion and wear of nozzle:
With the extension of working time, the nozzle will gradually be corroded by the tank liquid, and the physical impact of the liquid will also bring wear. After being corroded or worn, the nozzle nozzle and the inner flow channel surface will become bumpy, gradually deformed, and show signs of irregular increase through the hole, affecting the flow rate of the nozzle, the spray pressure and the shape of the spray. The corrosion and wear of the nozzle is an irreversible damage, and the problem can only be solved by replacement.
4. Temperature damage of nozzle:
If the temperature is higher than the rated temperature for a long time, the nozzle will be deformed due to high temperature, resulting in a change in the shape of the spray. Therefore, in the selection of the nozzle should be selected and the working temperature should match, if the nozzle is not suitable for the working environment at that time, it should be replaced in a planned way.
Correct installation and selection is equally important, if the nozzle installation is not correct, it will also bury the nozzle trouble. The common problems in the installation are: the nozzle installation washer deviated from the axis, the nozzle installation is too tight or too loose, the nozzle injection position and Angle are not adjusted well. Before the desulfurization system is put into operation, it should be carefully checked whether all the nozzles have been accurately installed in place, and the problems should be disassembled in time to solve the problems through secondary installation. If the installation has caused damage to the nozzle, a new nozzle should be replaced.