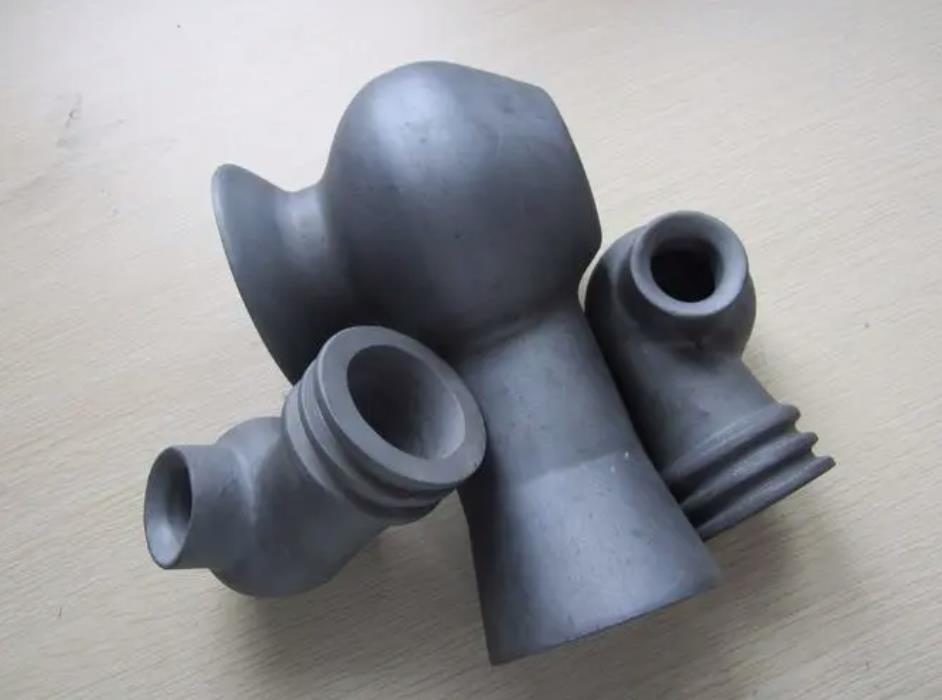
The following describes the main performance parameters of the desulfurization nozzle
1. Average particle size and droplet particle size distribution
The atomization performance of the nozzle depends on the inlet pressure of the slurry, the viscosity of the slurry, the surface tension and the nozzle structure parameters. When the nozzle inlet pressure is larger, the nozzle pressure drop is larger, the flow through the nozzle is larger, and the average diameter of atomized slurry droplets is smaller.
The average diameter of atomized droplets is usually expressed by the average diameter of the body area (Sauter average particle size). There are many factors affecting the average diameter of the slurry drop, so the equation can only be established by experiment. For tangential inlet nozzles, the formula for calculating the average diameter of the slurry is
DVS = 572.8 d1.589 sigma 0.594 0.220 Q - 0.537 mu
Type of DVS - volume, area average diameter, mu m;
d - nozzle aperture, mm;
σ - surface tension, N/m;
Mu - slurry viscosity, N.s/m2;
Q - Volume flow, m3/s.
The particle size distribution of spray droplets is very important for most applications, especially for wet desulfurization systems. For a particular working condition, the droplet particle size in the desulfurization tower has an optimal value. If the droplets can be sprayed with a high particle size uniformity with the optimal value, the investment can be reduced and the economic operation of the system can be achieved.
The uniformity of droplet size distribution is usually expressed by RSF:
RSF = (DV0.9 _DV0. 1)/DV0.5
In wet desulfurization, the average Sauter particle size of droplets is less than 2100μm, and the RSF is less than 1.
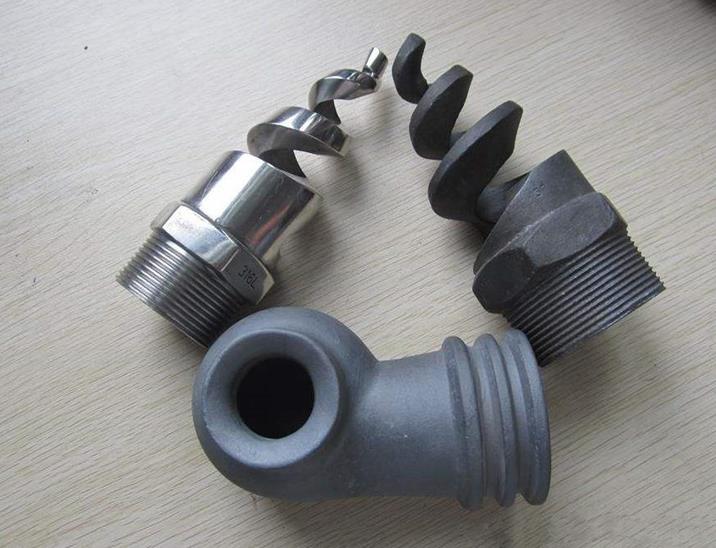
2, Nozzle pressure drop
Nozzle pressure drop refers to the pressure loss caused by the slurry passing through the nozzle channel, and the greater the nozzle pressure drop, the greater the energy consumption. The size of nozzle pressure drop is mainly related to nozzle structure parameters and slurry viscosity, and the greater the slurry viscosity, the greater the nozzle pressure drop.
The size of the pressure drop of the nozzle determines its working pressure, the smaller the pressure drop, the smaller the working pressure, and the smaller the power consumption of the circulating pump. At present, the working pressure of the double hollow cone tangential nozzle is roughly 0.5/0.7/0.8/0.85×105Pa.
3. Spray Angle
Spray Angle refers to the cone Angle of the liquid film hollow cone formed after the slurry is rotated from the nozzle. The main factors affecting the spray Angle are the various structural parameters of the nozzle, such as the radius of the nozzle hole, the radius of the rotating chamber and the radius of the grout inlet.
In the wet desulfurization system, the spray Angle of the desulfurization nozzle sprayed down is generally 90o, and the spray Angle of the desulfurization nozzle sprayed up is 120o. In the nozzle near the wall of the absorption tower, in order to avoid the erosion of the anti-corrosion material on the wall, the spray Angle of the desulfurization nozzle sprayed upward is also 90.
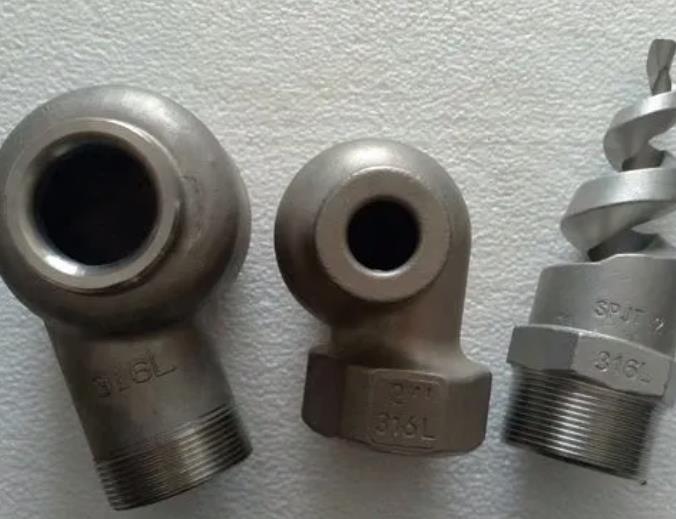
4, Nozzle flow
Nozzle flow rate refers to the volume flow rate through the nozzle per unit time, and the nozzle flow rate is related to the nozzle pressure drop, nozzle structure parameters and other factors. Under the same nozzle pressure drop condition, the larger the nozzle hole radius, the larger the nozzle flow. The calculation formula of nozzle flow rate is as follows:
Q = CD PI rD rD SQRT (2 r Δ P/rho)
Where, Q - nozzle flow, m3/s;
rD - nozzle hole radius, m;
CD - flow coefficient;
△P - Nozzle pressure drop, Pa;
- Slurry density, kg/m3.
The flow of the nozzle will eventually affect the economy of the desulfurization system, in a given absorption tower, the selection of a large flow nozzle can reduce the total number of nozzles required, thereby reducing the cost of the system, the large flow nozzle has fewer restrictions and good anti-blocking performance, which can effectively save operation and maintenance costs. However, the selection of large flow nozzles is also sacrificed, and the droplet size needs to be increased, so the maximum flow rate acceptable for different nozzles is limited by the atomization effect of this nozzle.
For the nozzle flow in wet desulphurization at about 50 m3 / h.
5, Free flow diameter
Free flow diameter refers to the maximum diameter of the nozzle that allows spherical impurities to pass through. The larger the free flow diameter, the better the performance of the aromatic blockage.