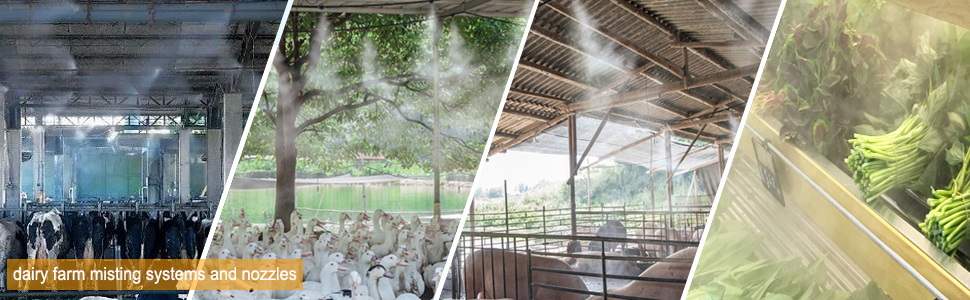
Fine misting nozzles are carefully machined from solid materials such as 304 stainless steel or brass. Users can also choose SS stainless steel, BRASS brass, ceramics and other materials according to different application environments, effectively meet the requirements of high temperature resistance, corrosion resistance, wear resistance, impact resistance and so on. This series of nozzles does not require air assistance, and the system is simple; Spray spray point is fine, misting is full, energy saving and water saving, low cost, good effect; The nozzle is not blocked, no water leakage, internal automatic cleaning, stainless steel nozzle treated by advanced forging process, durable, is 2.5 times the life of similar nozzles.
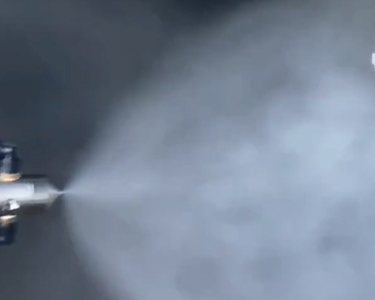
The fine misting nozzle is to pressurize the treated water to 5~7MPa through the high-pressure plunger pump, and then transport it to the special high-pressure micro-fog nozzle evenly distributed in the workshop by the high-pressure pipeline. After passing the spiral channel of the nozzle, the water is atomized into very fine water mist particles and sprayed into the air from the nozzle hole. The water mist particles with a large specific surface area exchange heat and humidity with the air. Achieve the purpose of humidifying the air. This process increases the relative humidity of the air and decreases the temperature of the air at the same time.
Seven reasons for poor misting of fine misting nozzle:
1. Corrosion and wear
The inlet and outlet of the nozzle are worn or stretched due to long-term consumption, 1 especially in the nozzle made of plastic materials.
2. Block
Some magazines or solidified liquids that need misting clog the pipes.
3. Corrosion
The internal structure of the nozzle is not smooth due to the corrosion of various chemicals.
4. Temperature damage
Overheating will have a certain damaging effect on nozzle materials designed for non-high temperature applications
5. Bond
Spray, mist, or chemical buildup caused by liquid evaporation on the inner or outer material of the nozzle nozzle edge 1 can clog the nozzle nozzle or internal flow path with a dry solidifying layer
6. Incorrect installation
Off-axis gaskets, over-tightening or other positional changes can have adverse effects
7. Accidental injury
During installation and cleaning 1 the nozzle may be accidentally damaged due to the use of incorrect tools