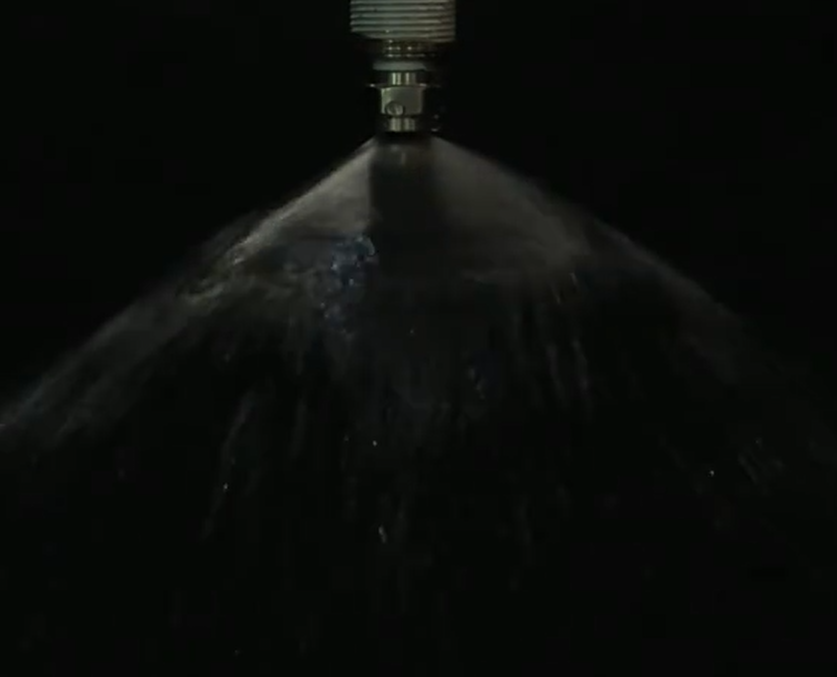
Sprayer nozzle is the most important part of atomizing liquid, which plays a decisive role in spray quality. The sprayer nozzle mainly has three types: vortex nozzle, fan nozzle and impact nozzle.
(1) Vortex nozzle
It is characterized by a guiding part in the nozzle, through which the high-pressure liquid produces spiral motion. According to the different structure, the vortex nozzle can be divided into three types: tangential centrifugal nozzle, vortex vane nozzle and vortex core nozzle.
① Tangential centrifugal nozzle. The nozzle is composed of a nozzle cap, a spray hole piece, a washer and a nozzle body. The nozzle body is processed into an inner cavity with a cone core and an infusion ramp tangent to the inner cavity. There is a spray hole in the center of the spray hole plate, and the aperture is 0.7mm, 1.0mm, 1.3mm, 1.6mm (NJ130-75). A cone core vortex chamber is formed between the inner cavity and the spray hole sheet. In order to prevent corrosion, the parts that touch the liquid in the nozzle are made of copper or plastic.
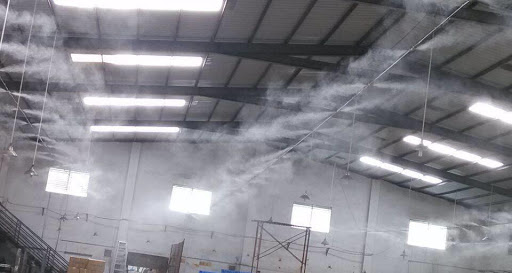
The operation principle of tangential centrifugal nozzle high-pressure liquid flow from the spray rod into the infusion ramp, because the cross-sectional area of the ramp becomes smaller, the flow rate activity increases, the high-speed liquid flow along the ramp into the vortex chamber in the tangential direction, and makes high-speed spiral movement around the cone. When near the jet hole, because the turning radius is reduced, the circumferential velocity of the liquid particle is larger. The liquid particle emitted by the jet hole has two speeds: one is the traveling speed Vc parallel to the center line of the jet hole, and the other is the tangential speed Vt of high-speed rotation. The composition speed V of the two is the movement direction of the liquid particle practice, and there is an Angle α between it and the center line, and 2α is the fog cone Angle. Because the liquid eruption process is continuous, therefore, the liquid from the spray hole, into a conical scattering film, the farther away from the hole, the thinner the liquid film, resulting in fracture into fragments, agglomerate into droplets. Due to the effect of air resistance, the large droplets continue to break up into finer droplets.
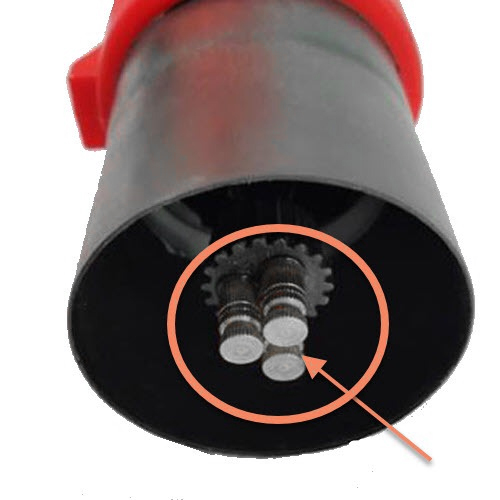
Tangential centrifugal nozzle structure is simple, not easy to plug, but the degree of atomization is poor, the diameter of the droplets is generally greater than 250μm, and it is mostly used for manual sprayer. In order to travel power and to be used with the larger motor sprayer, in addition to manufacturing a single nozzle, there are also two nozzle and four nozzle. For example, the tangential centrifugal nozzle used in conjunction with the Gongnong-36 motor sprayer is a dual or four-nozzle combination nozzle.
② Vortex vane nozzle. It consists of a nozzle cap, nozzle blade, gasket, vortex blade, and nozzle body, as shown in Figure 8-16. There are two shell shaped oblique holes punched symmetrically in the circular direction on the vortex plate. A washer is sandwiched between the nozzle plate and the vortex plate, thus forming a vortex chamber. The atomization principle of the vortex vane nozzle is similar to the operation principle of the tangential centrifugal nozzle, which is characterized by the pressure liquid entering the vortex chamber through the inclined hole of the vortex vane and producing high-speed spiral motion. The nozzle operating pressure is 300 ~ 400kPa, the atomization performance is good, the atomized liquid diameter is 150 ~ 300μm, the structure is simple, and it is mostly used for manual sprayer.
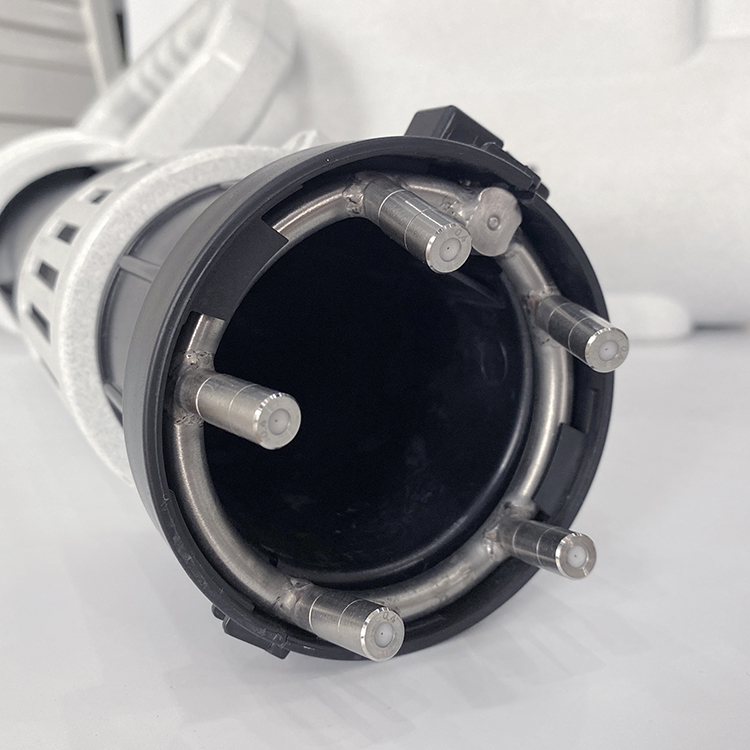
③ Vortex core nozzle. It consists of a nozzle cap, a vortex core, and a nozzle body, as shown in Figure 8-17. The operating principle is the same as the tangential centrifugal nozzle, the liquid is injected from the liquid pipe or nozzle during operation, and the activity is along the chute with spiral Angle, generating centrifugal force, so that the liquid is sprayed from the spray hole in a fog cone, and the surrounding air is hit into a mist droplet with a diameter of 150 ~ 300μm in the centrifugal rotation, and the operating pressure is generally 150 ~ 300kPa. The structure is more complex.