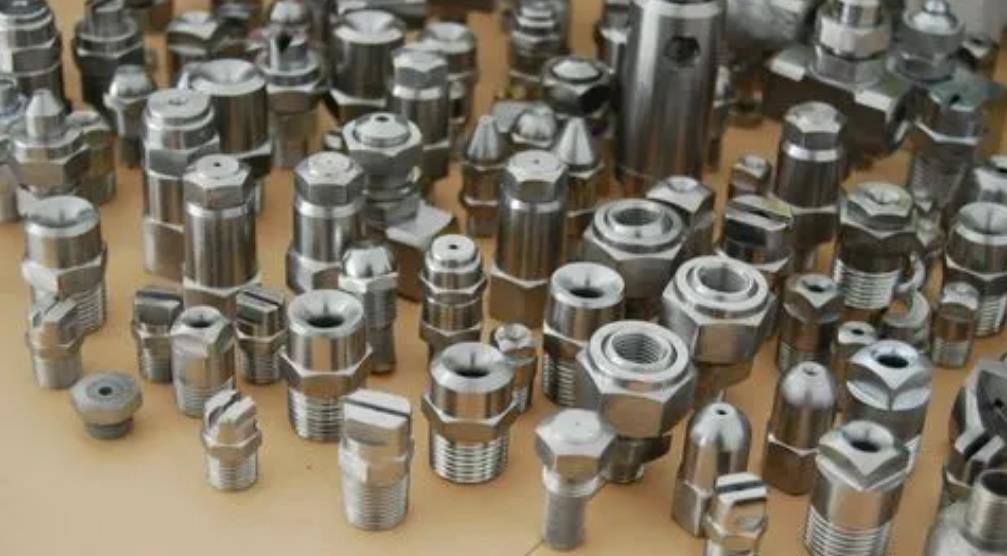
The spray nozzles need to be serviced, regularly inspected, cleaned and even replaced in order to ensure the quality of the final product and maintain the economic efficiency of the production process. Customers can schedule regular service or replacement depending on the spray nozzle's use, spray liquid and spray nozzle material.
If the spray nozzle does become clogged, only a soft brush or toothpick can be used to clean it and the cleaning process should be very careful, even using a wooden toothpick to clean the spray nozzle may also distort the orifice.
spray nozzle fittings include pipe thread fittings, solenoid valves and liquid filters and pressure gauge fittings.
Spray nozzle product classification
Spray nozzles can be divided into two categories: burner spray nozzles (military, civilian), non-burner spray nozzles;
According to the function of the spray nozzle spray nozzle can be roughly divided into: spray spray nozzle, oil injection burner, sand blast spray nozzle, and special spray nozzle.
According to the material classification, it can be divided into: metal spray nozzle, plastic spray nozzle, ceramic spray nozzle, alloy spray nozzle.
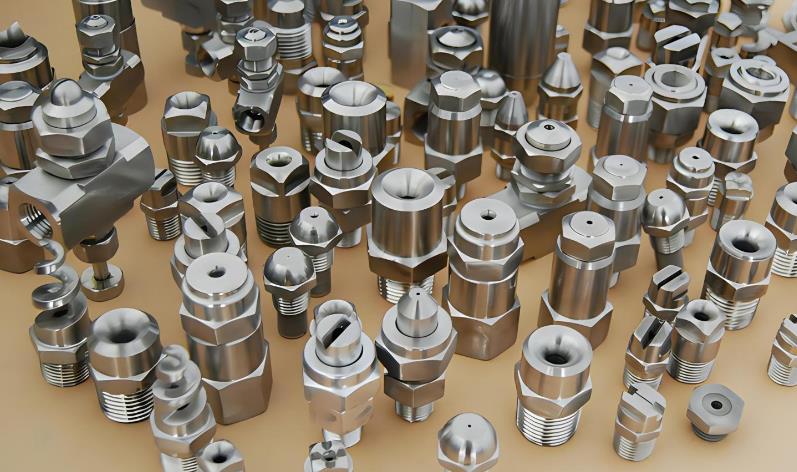
If the application environment requires corrosion protection, it is necessary to avoid the use of metal spray nozzles. For strong corrosive media such as sulfuric acid and hydrochloric acid, spray nozzles made of nylon plastic can be used. Stainless steel can also effectively prevent corrosion.
According to industry classification, it can be divided into: petrochemical spray nozzles, agricultural spray nozzles, textile spray nozzles, paper spray nozzles, printing spray nozzles, environmental protection (desulfurization, denitrification, denitrification, dust removal, etc.) spray nozzles, spraying spray nozzles, steel metallurgy spray nozzles, electronic spray nozzles, food spray nozzles.
According to the shape classification, it can be divided into hollow cone spray nozzles, solid cone spray nozzles, square spray nozzles, rectangular spray nozzles, elliptical spray nozzles, fan spray nozzles, column flow (DC) spray nozzles, two-fluid spray nozzles, multi-fluid spray nozzles and so on.
Five functions of spray nozzle
The tasks of spray nozzles in different factories and equipment in the world are diverse, but when studying spray nozzle performance, you should first understand the five functions that spray nozzles usually need to have:
(1) The spray nozzle meets the liquid flow requirements: under a certain pressure, the spray nozzle should provide a specific flow rate. Flow is usually expressed in liters per minute (L/min).
(2) The spray nozzle produces a spray shape: the common spray shapes are full cone, hollow cone, fan and needle.
(3) atomized particles produced by the spray nozzle: according to the liquid sprayed, the type of spray nozzle, the flow rate and pressure are different, the range of atomized particles is 20~10000um.
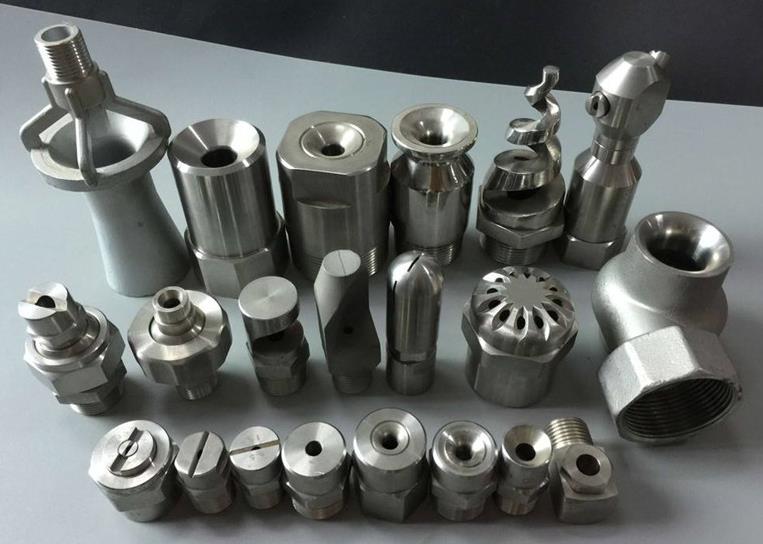
(4) The spray nozzle produces a striking force: the striking force refers to the impact force of the spray on the target surface, expressed in kilograms of force/square centimeter (MPa). It depends on a number of factors, including flow rate, spray shape, spray nozzle type, spray distance, and pressure.
(5) The spray nozzle provides spray speed: the liquid pressure is transformed into a high-speed jet, forming a certain speed, expressed in meters per second (m/s). High pressure cleaning; Both descaling and flue gas cooling of steel rolling have certain requirements for liquid velocity.
Application field of spray nozzle
spray nozzles are widely used in the industry, with materials ranging from stainless steel and plastics to silicon carbide, polytetrafluoroethylene, PP (engineering plastics), aluminum alloy and tungsten steel.
Generally speaking, spray applications can be divided into the following four categories:
(1) Cleaning, washing, rinsing: including high pressure descaling during hot rolling and medium and high pressure cleaning of products, vehicles and equipment. Low pressure flushing and rinsing are also included.
(2) Coating: Spray coating applications include spraying anti-rust agents, plastic coatings, release agents, lubricants, protective films and wetting, curing, etc.
(3) Cooling: In this type of application, the spray is used to cool solid targets such as billet cooling for continuous casting steel, roll cooling, assembly cooling and treatment equipment, tank cooling, and circulating water cooling.
(4) Special applications: including dust control, air and flue gas spray, spray drying, granulation, spray humidification, etc.
Saving time, money and energy in spray nozzle applications
Saving time, saving money and saving energy is the eternal goal of all industrial enterprises to pursue, however, the spray nozzle used in the steel industry, relative to other equipment and components, is small, and its impact on process operation and maintenance is mostly indirect, so whether the spray nozzle used is saving time, saving money and saving energy is easy to be ignored or not treated correctly.
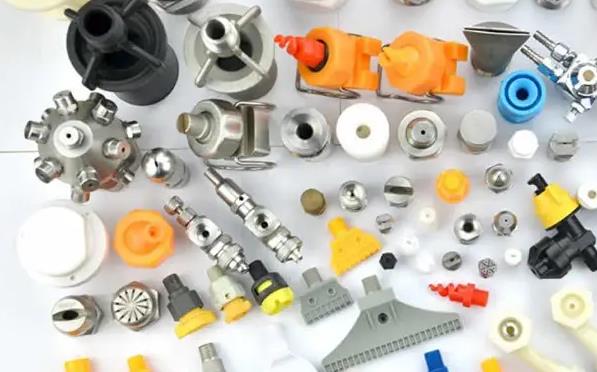
Time-saving performance in three aspects: first, easy to replace; Second, long life requires fewer replacement times; The third is timely replacement according to the standard, for example, the continuous casting spray nozzle of an individual factory is not replaced in time according to the standard, which appears to save time on the surface, but because the spray nozzle performance is seriously poor, steel leakage and waste products lead to more time required for maintenance and sorting.
Saving money is more need comprehensive balance calculation: need to calculate the cost of tons of steel or even tons of materials is the real savings. Cheap does not necessarily save money, and excess features are wasteful.
Energy saving is the area where the spray nozzle can have a greater impact: for example, when the traditional water spray nozzle is used for flue gas cooling and dust removal of 20t converter, the water spray volume is 150~200t/h, and the spray nozzle can save at least 1/3 water after updating; The gas-water atomizing spray nozzle used in slab continuous casting machine, the early design of each spray nozzle needs about 80m3/h of compressed air, the least also needs 20~30m3/h, and the current most advanced gas-water atomizing spray nozzle compressed air consumption of less than 10m3/h.