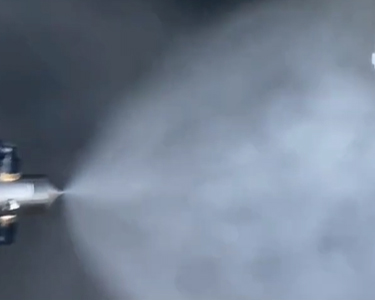
Introduction to ultrasonic atomization spraying
Ultrasonic atomizing spray is a unique spray technology, which is based on ultrasonic atomizing nozzle technology. The sprayed material is first liquid state, liquid can be solution, sol, suspension, etc. The liquid coating is atomized into fine particles through the ultrasonic atomizing device, and then evenly coated on the substrate surface by a certain amount of current carrying gas, so as to form a coating or film. Compared with the traditional pneumatic two-fluid spraying, ultrasonic spray can achieve better uniformity, thinner coating thickness and higher accuracy. At the same time, because the ultrasonic nozzle does not need pressure assistance to atomize, the use of ultrasonic spraying can significantly reduce the spray of paint during the spraying process, to achieve the purpose of saving paint, the utilization rate of ultrasonic spraying paint is more than 4 times that of traditional two-fluid spraying.
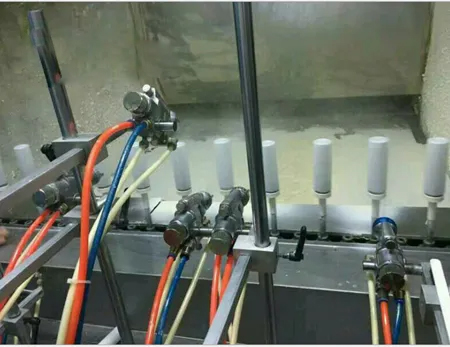
The principle of ultrasonic atomization spraying
High-frequency sound waves are converted into mechanical energy by a piezoelectric transducer, which is then transferred to a liquid. This longitudinal upward and downward vibration produces standing waves in the applied liquid film at the tip of the ultrasonic nozzle, where the amplitude of these waves can be controlled by a power generator. These stationary liquid waves can extend upward from the tip of the ultrasonic nozzle, and when the droplets leave the atomizing surface of the nozzle, they are broken down into a fine fog of uniform micron or even nanoscale droplets.Advantages of ultrasonic atomization spraying
1. High stabilityUltrasonic spraying is made of high-performance titanium alloy and stainless steel, strong adaptability, corrosion resistance, no pressure, no noise, no nozzle wear and blockage, high atomizing particle uniformity.
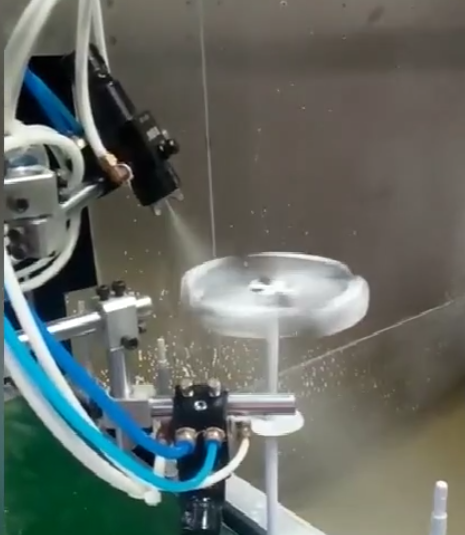
2. Energy saving and environmental protection
Ultrasonic spraying atomizing impact is very small, will not cause liquid splash, can reduce the waste of raw materials and air pollution caused by reverse spraying.
3. Molding is controlled
Precise control of atomizing flow, low flow continuous spray, spray shape is easy to control and shape (increase spray robot arm), suitable for industrial fields. Through the combination, the atomizing volume can meet any requirements of the user.
4. Easy to maintain
The liquid is transported to the nozzle by gravity or low pressure pump to achieve continuous or intermittent atomizing. No cooling water is required when atomizing, low energy consumption, simple equipment, low failure rate, daily maintenance free.
5. Wide range of applications
The size of atomized particles is determined by ultrasonic frequency and has nothing to do with nozzle diameter. It is difficult to clog the nozzle while maintaining ultrasonic oscillation during atomizing. The nozzle can be applied to a variety of solutions, and can even atomize sewage, chemical liquids and oil slime.
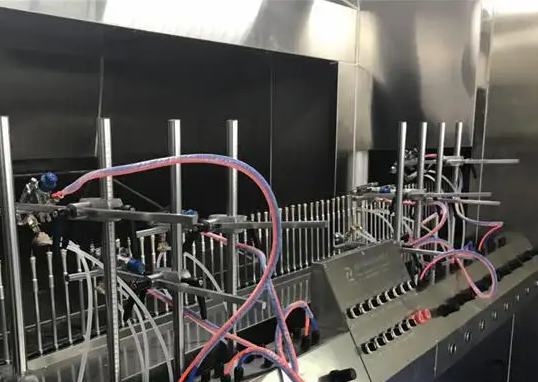
Introduction to traditional spraying:
Traditional spraying is a coating method by spraying gun or dish atomizer, with the help of pressure or centrifugal force, dispersed into uniform and fine droplets, applied on the surface of the coated material. It can be divided into air spraying, airless spraying, electrostatic spraying and various derivative methods of the above basic spraying forms, such as large flow and low pressure atomizing spraying, thermal spraying, automatic spraying, multi-group spraying and so on.Characteristics of traditional spraying:
1. Use the kinetic energy atomizing of two fluids, gas and liquid
2. Spray impact force is large, will cause splashing and waste of raw materials
3. Poor uniformity of atomized particles
4. Atomizing particle size is determined by the nozzle diameter
5. When the nozzle is very thin, it is easy to block the nozzle
6. Can not accurately control the spray flow, can not continue to spray at low flow
The difference between ultrasonic spraying and traditional spraying:
Ultrasonic atomizing spray is an advanced atomizing technology, which combines the advantages of ultrasonic and spray technology and brings revolutionary changes to modern manufacturing industry. Through ultrasonic atomizing, we are able to achieve a more uniform and fine coating, thereby improving product quality and performance.
In the process of ultrasonic atomizing spraying, the vibration effect of ultrasonic can rapidly atomize the liquid coating into tiny particles, and spray it to the surface of the substrate through high-speed air flow. This spraying method not only improves the utilization rate of the coating, but also enables a more uniform coating distribution. At the same time, the vibration effect of ultrasonic waves can also form small gaps in the coating, making the coating more breathable, wear-resistant and corrosion-resistant.
Compared with the traditional spraying technology, ultrasonic spray has a wider range of applications. It can be used not only for the spraying of common materials such as metals and plastics, but also for the spraying of coatings with high viscosity and high solid content, as well as the spraying of workpieces with special shapes and structures. In addition, ultrasonic spray also has the advantages of simple operation, high production efficiency, environmental protection and energy saving, so it is widely used in automotive, electronics, aerospace and other fields.
Ultrasonic atomizing spray is an efficient, fine and environmentally friendly spraying technology, which can not only improve product quality and performance, but also bring more sustainable development for enterprises.