One, spiral nozzle introduction:
Spiral nozzle is also called desulfurization nozzle, anti-blockage nozzle, large flow nozzle, dust nozzle, corrosion resistant nozzle, is a solid conical or hollow conical spray nozzle, spray Angle range can be 50°-170°. Fluid flow rates range from 5.5 to 4140 l/min at 3 bar. The compact nozzle has a clear flow channel to minimize fluid obstruction, allowing fluid to flow in a given size pipe.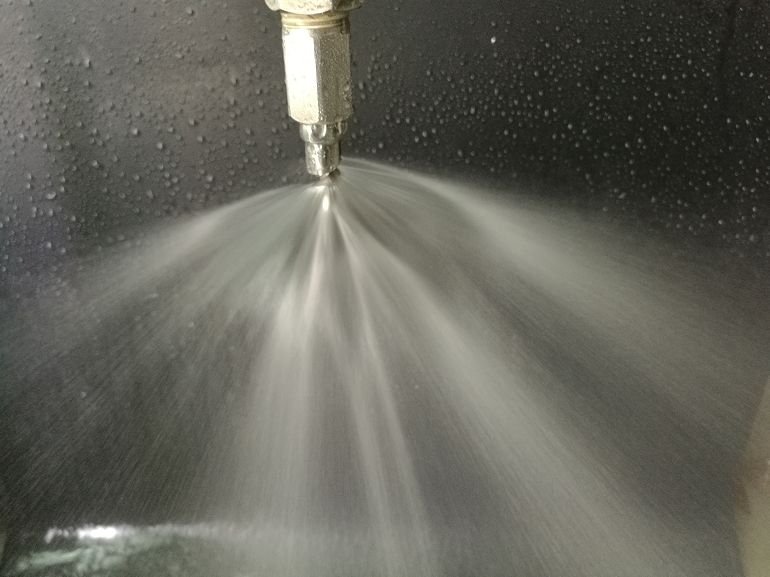
Two, the working principle of the spiral nozzle
When a certain pressure and velocity of liquid flowed from the top downward spiral nozzle, the outer part of the liquid impact the nozzle Angle of helical surface, leave so as to change the direction of jet nozzle, hit the bottom, for jet nozzle opening definition liquid surface, as shown in figure 1 a helicoid E, and E should be sprayed on helical surface E, defined in the perpendicular to the axis of the jet distance, The plane composed of droplets is the atomization surface, as shown in Figure 1B plane F. From the microscopic point of view, the atomization surface should be a concave sphere due to the existence of the length of the spiral cone of the nozzle, but relative to the long atomization distance, the length of the spiral cone can be ignored, so it can be approximately considered as a plane.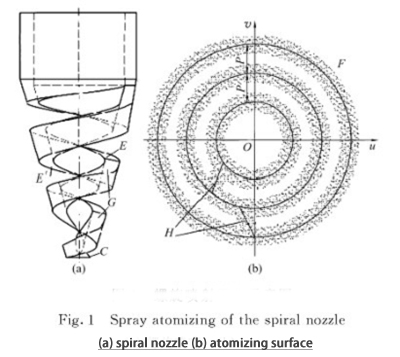
Working principle of spiral nozzle due to different layers of the cone spray surface streamline and the different spiral Angle, Angle of nozzle axis and Angle decreases step by step, and the atomization surface shape can be formed with the same spacing of concentric circles, the general design of atomization surface is composed of 2 to 4 concentric circles of mutual connection, when the reverse jet plane geometry structure is projected onto the spiral nozzle, Since there are the same helical angles in the same spiral plane, but the helical angles in different circles are different, the helical nozzles between the adjacent spiral planes must have obvious conversion surfaces, as shown in FIG. 1A G. Therefore, obvious linear transition zones can be seen on the atomization surface, as shown in FIG. 1B H. Due to the existence of surface G, the strength of the spiral nozzle has the disadvantage of stress concentration, and the droplet distribution on the atomizing surface will overlap at H, which is not conducive to the uniform distribution of atomized droplets.
A new type of spiral nozzle with involute atomizing surface is presented. According to the requirements of the atomization plane, the beginning and end of the involute were optimized. The spiral nozzle was mapped from the moving coordinate system to the fixed coordinate system, and the spatial geometric model of the spray profile was derived. The effectiveness of the proposed geometric model of the spray profile of the specific involute atomization surface was verified by Matlab simulation. It provides a theoretical basis for the design and manufacture of spiral nozzles. Because of the cancellation of conversion surface, the new spiral nozzles have a reasonable stress distribution and a more uniform spray distribution, which can achieve better results under the condition that the circular degree of atomization surface is not strictly required.
The principle of the spiral nozzle is that the liquid forms spray after tangency and collision with the spiral surface
The principle of a spiral nozzle is to shoot liquid from a spiral into a spiral metal orifice. The spiral nozzle breaks the traditional spray mode in which the flow into the relatively fine concentric rings will form a conical spray shape. The spray produced according to the principle of spiral nozzle is uneven spray shape rather than complete conical spray shape.
The spray principle of spiral nozzle is to spray uneven spray shape
The principle of the spiral nozzle is to use impact dispersion spray out, the internal spiral nozzle is not an unimpeded channel, water flow is by hitting the layered interface of the spiral, so that the product layer spray effect. The conventional solid nozzle will have a blade inside, so that the liquid flows clockwise or counterclockwise through the guide action of the blade, and the liquid produces centrifugal force due to the action of water pressure, so the complete conical spray is ejected.
The spiral nozzle structure can eject at least 3 to 4 spray stratified interfaces
Solid conical spiral nozzle effect drawing

Hollow conical spiral nozzle effect drawing
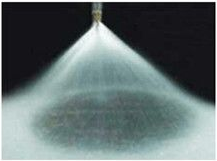