Cleaning in place (CIP for short), also known as cleaning positioning or positioning cleaning. CIP cleaning system is widely used in beverage, dairy, fruit juice, fruit pulp, jam, wine and other food and beverage production enterprises with a high degree of mechanization. Let's learn about it today.
Equipment composition of CIP cleaning system
CIP cleaning system is determined according to the number of cleaning points, CIP cleaning system is mainly composed of acid tank, alkali tank, water tank, concentrated acid concentrated alkali barrel, heating system, diaphragm pump, high and low liquid level, online acid and alkali concentration detector and PLC touch screen control system. The acid tank, alkali tank, water tank for insulation tank, in addition to the acid and alkali tank also has a stirring system.
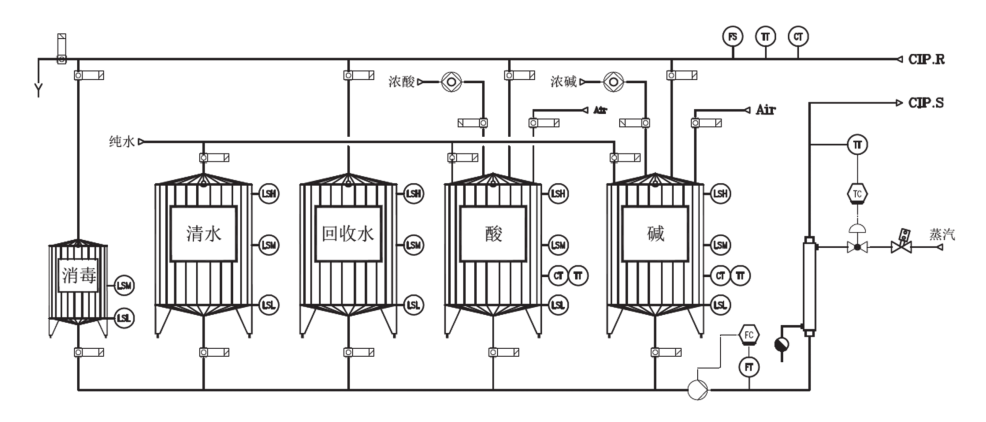
The core of CIP cleaning system is CIP cleaning station, which usually has two cans, three cans, four cans and five cans. At present, four cans (acid tank, alkali tank, water tank and recycling tank) and five cans (alkali tank, acid tank, hot water tank, recycling tank (neutralization tank), clean water tank) are in the majority. The solution stored in each cleaning tank is different, and different cleaning processes will be designed and different detergents will be used according to cleaning needs.
.png)
Single tank system
.jpg)
Double tank system
.png)
Three pot system
02 CIP cleaning process
.png)
General principles of cleaning process:
1. The general process is a three-step process (water rinse, alkali wash and final shower)
2. Aseptic liquid dispensing process adopts five-step cleaning (water rinse-alkali rinse-water rinse-acid rinse-final leaching)
3. Water washing usually uses drinking water or recycled final shower water. The water temperature can be adjusted according to different residues. Generally, the water temperature is controlled between 60 ℃ and 80℃
4. Caustic washing usually uses 1.0~2.5%NAOH solution, and the caustic washing solution can be recycled without cross-contamination
5. Always use 1.0 to 2.0% nitric acid for pickling
6. The final spray shall be purified water, and the sterile solution shall be injected water
.png)
Example of CIP cleaning in five steps
The requirements for cleaning agents are as follows:
1. · Moisture Function
2. · Dissolve and remove dirt
3. · Prevent scale formation
4. · Soluble in water
5. · easy to wash
6. · Do not corrode the device surface
7. · non-toxic
8. · effective
9. · Biodegradable
Commonly used detergents are acid, alkali and sterilizing detergents. Its advantages and disadvantages are as follows:
1. The advantages of acid and alkali detergent: Pickling can remove calcium salt and mineral oil residues through chemical reactions. Alkaline washing can remove residues such as fat and protein by saponification.
2. The disadvantages of acid and alkali detergents: they are harsh to the skin. Poor washability.
3. The advantages of the sterilizer: It has a rapid sterilization effect and is effective for all microorganisms. Generally non-toxic after dilution; Not affected by water hardness; Forming a film on the surface of the equipment; Concentration easy to determine; Easy to measure; Can remove stench.
4. The disadvantages of sterilizers: They have a special flavor; Need certain storage conditions; Different concentrations of bactericidal effect is different; Easy to freeze when the temperature is low; Improper use can cause side effects; The bactericidal effect of mixed filth decreased obviously; Easy to stain the environment and leave traces when falling.
04 Influencing factors of CIP cleaning
The influencing factors of CIP cleaning can be considered from the cleaning theoretical model-TACT model, which is also the four factors model of cleaning effect.
CR=Ti+A+C+Tc
CR: cleaning effect, %;
Ti: time, %, mainly refers to the time of contact and action with the cleaned surface;
A: Mechanical action, %, generally accounting for more than 50%, mainly pressure, flow rate, etc.
C: chemical action, %, mainly the type and concentration of cleaning agent, etc.
Tc: temperature action, %; Mainly cleaning agent temperature, with the type of dirt and viscosity.
.jpg)
1: Time Ti
Generally speaking, the longer the cleaning time, the better the effect. But in the industrial production must ensure the production rate, usually cleaning time is 2 ~ 3 times of complete coverage time. Every step of the whole in-place cleaning process takes the cleaning time as the running time. It should be noted that the cleaning time of lye is generally greater than that of acid, but the longest is generally no more than an hour.
2: Mechanical action A
Mechanical effect occupies more than 50% of the whole cleaning effect, so it needs to be focused on, often pay attention to the flow rate, flow rate, pressure these factors, so as to ensure the cleaning effect.
.png)
For equipment tank need to use spray ball, pipe valves need to ensure that the fluid is in a turbulent state.
Generally ensure that the cleaning flow rate can reach 1.5m/s, do not exceed 3m/s. 1.5m/s basically belongs to the economic flow rate of fluid, which is preferred.
03 Chemistry C
For chemical action, focus on the selection and concentration of cleaning agent. Suitable detergent can be selected according to detergent's decontamination ability and the difficulty of residual rinsing.Seven basic principles of detergent selection
(1) Efficient cleaning, with broad spectrum;
(2) do not advocate the use of household detergent, because its composition, quality, microbial, etc.;
(3) select detergent with simple components and definite content of components;
(4) Easy to check;
(5) Good stability, low toxicity, safe use;
(6) Compatibility with equipment or environmental materials;
(7) Lower fees.
Acid washing will use mild, low concentration of acid solution, such as HNO3, H3PO4 and citric acid, do not use HCl (serious corrosion of stainless steel); Lye generally adopts NaOH, Na2CO3, NaHCO3, Na3PO4 and Na2SiO3. It should be noted that if Na2SiO3 is not cleaned properly, white precipitation of Ca3(PO4)2 will be generated when the product is heated.
Acid concentration is generally 1.0~2.0%, base concentration is generally 1.0~2.5%.
.png)
4: Indicates the temperature Tc
Here, common HNO3 and NaOH are taken as examples to establish the trend chart of corrosion ability and cleaning effect of HNO3 and NaOH with the change of cleaning temperature.
.png)
It can be seen from the figure that the corrosion ability of nitric acid increases with the increase of temperature, while the cleaning effect tends to be gentle. It can be seen that the cleaning temperature of nitric acid should not be too high, 60-105℃. With the increase of temperature, the corrosion ability of NaOH tends to be gentle, while the cleaning effect increases. It can be seen that the higher the cleaning temperature of NaOH is under certain conditions, the better. For most of the cleaning agent, we can in a certain temperature range temperature rise every 10 ℃, the chemical reaction rate increased by 1.5 to 2 times, is important to note that although the temperature increase, cleaning speed, the dissolution rate will be increased, but the temperature is too high, the residual proteins may be modified, lead to equipment is more difficult to clean. So it's not that higher temperatures are better. Under normal circumstances: when the temperature reaches 80℃, the temperature rises again, the cleaning time basically does not change, so the cleaning liquid temperature is generally controlled at 60~80℃.
5. Other factors
In addition to the four points mentioned above, water quality and pipeline design also have a certain impact on CIP cleaning..png)
Examples of water quality requirements
.png)
.png)
Examples of pipe design requirements
05 Evaluation of CIP cleaning effect
In principle, the sampling location of CIP cleaning effect should be the most serious and most difficult part of the structure to clean. Example:1, FM (filling machine) : up and down filling pipe, A\B\C valve, etc
2, UHT: product entrance → homogenizing machine section, homogenizing machine → insulation pipe, insulation pipe outlet, etc
The evaluation of CIP cleaning effect can refer to the following standards:
Number | project | Standard |
1 | smell | Fresh, indistinguishable odor, for special processing or special stage to allow a slight odor but does not affect the safety of the final product and its quality. |
2 | visual | Clean the surface bright, no water, no film, no dirt or other; When water flows over the surface, there are not too many broken marks in the water trace |
3 | health | When touching the surface with fingers, there is no greasy and rough feeling; Wipe the surface repeatedly with a new white paper towel for stains and discoloration |
4 | Production capacity | After CIP treatment, the production capacity of the equipment changes obviously. |
5 | microbial | Health indicators microbial indicators to meet the relevant requirements; It can not cause the improvement of other health indicators of the product. |
06 CIP common defects and controls
Item | Main defects | Cause analysis | The control method |
1 | Insufficient cleaning temperature, time, concentration or flow rate | Because the calculation method is not correct |
① Temperature, time and concentration should be calculated at the final exit point ② The flow rate should be calculated at the point of maximum pipe diameter |
2 | CIP pipeline after CIP cleaning, there are still residues | The recovery liquid (acid and alkali) in the deployment section is not replaced in time, resulting in repeated pollution of CIP pipeline or incomplete CIP |
(1) It should be replaced every 48 hours (subject to cleaning effect) ② Carry out CIP thoroughly |
3 | CIP piping parts can't be cleaned thoroughly | Due to inadequate COP, parts that should be removed and cleaned were not thoroughly cleaned and disinfected |
"(A) Those which should be removed and washed daily are: (1) Filling section: lower filling pipe, leakage valve (2) Homogeneous section: buffer pipe, leakage parts ③UHT section: balance barrel, filter and leakage parts (4) Deployment section: filter, some valves and leakage parts (B) Those regularly removed and washed are: ① Filling section: upper filling pipe, A, B, C valve ②UHT section: insulation pipe; VA, VB valve: VA: -Va2 section: Va2 to balance bucket section, etc (3) Deployment section: some valves, top cover air filter" |
4 | There is still excess scale in CIP pipeline after CIP | Do not do regular special detergent cleaning or cleaning is not thorough | The CIP pipeline should be descaled once a week to remove residual scale completely (with surfactant). |
5 |
① Gaskets and sealing rings cause heavy pollution ② The probe of each instrument pollutes the product (3) Elbow, dead corner, joint fouling products |
① Due to long-term corrosion by high temperature acid and alkali, gaskets and sealing rings are easy to deformation, damage, carbonization and leakage ②Meter probe scale, oil leakage, loosening (3) Elbows, dead corners and joints are not easy to clean |
(1) CIP cleaning pipes and spare parts should be checked frequently, damaged aprons should be replaced in time and timely maintenance should be done: (2) Regular cleaning of dead corners, (elbow, joint, probe) residual scale. |
6 | Unable to find relevant CIP records, unable to timely make accurate analysis of quality accidents | Incomplete and accurate CIP cleaning records are not established | A complete and accurate CIP cleaning record should be established for inspection and reflection to better improve the relevant process and equipment. |